Understanding AC and DC in Welding
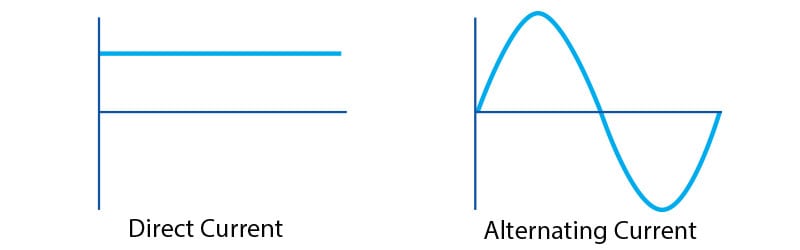
Welding and Polarity
Welding is the process whereby metals are melted and a filler used to help create a join, or the weld. The most commonly used welding processes are arc welding, which uses electrical currents; and gas welding. Not all metals will weld properly, as stainless steel can distort or crack, and alloys can prove tough if the exact chemical composition it is made from, is not known.
Straight and reverse polarity are common terms in welding. Straight polarity is another way of saying electrode negative, and reverse polarity is positive electrode. A welder needs to know how polarity works, so they can choose the right electrode for that polarity to achieve the best results. Welding rods are labelled as to the polarity required to use for it.
Welding in DC
DC stands for Direct Current where the charge travels in one direction all of the time returning a constant polarity. In welding there are two electrode connections, a direct current electrode positive, and a direct current electrode negative. Electrode negative or straight current (DCEN) is faster in its process, as the melt-off of the electrode is quicker. Straight current will produce less heat than DCEP (or positive electrode), therefore it is used more on thinner substrates. In DC reverse polarity the electrode is positive and the current flows from the workpiece to the electrode.
Best types of welding using DC
Mild Steel Electrode
Hard facing
Single carbon brazing
Build up of heavy weld deposits
Stainless steel TIG welding
Advantages of DC Welding
For stick welding DC has more to offer than AC. DC features include:
- Easy to start
- Less outages and sticking
- Less splatter
- Better weld appearance
- Better with overhead and vertical welding
- Gives a smoother arc
- Great for beginners learning to weld
- Straight polarity welds a lot of thinner metals better than AC
Best uses of DC welding are for:
Overhead
Vertical
Cast iron
Rivets
Heavy aluminium
Sheet metal
Low hydrogen
Arc bronze rod
Welding in AC
AC stands for Alternating Current and means that the electric charge travels in one direction half of the time and the opposite direction for the other half. Electrode positive or reversed polarity (from the AC current) will typically result in a deeper penetration through a metal. Some electrode shields can function using either polarity, while others require just one polarity. Choosing the correct polarity is important to ensure you get the best result from welding, otherwise you may encounter overheating, poor penetration, non-uniform beading, splatter, lack of arc control, or the electrode burning out.
Best types of welding using AC
High frequency Tig Welding on Aluminium
Downhand on heavy plate
Advantages of AC Welding
- Works with magnetized materials
- For use on aluminium
In Summary
Using DC is the most common type of welding, and is great for general maintenance and jobbing work. With DC welding it typically has much more to offer than AC welders, but AC is critical for high frequency tig welding on aluminium. The vast majority of electrodes can be used for both AC and DC welding, and many welders have the terminals marked or directions on how to change polarity, some have switches to easily change, and on others some cables may need to be changed. Happy welding!
Image credit: www.electricaleasy.com